Looking to Reduce Costs? Check Your Medical Device Design
Trelleborg’s new Rapid Development Center aims to help medical device companies take costs out of manufacturing.
August 24, 2021
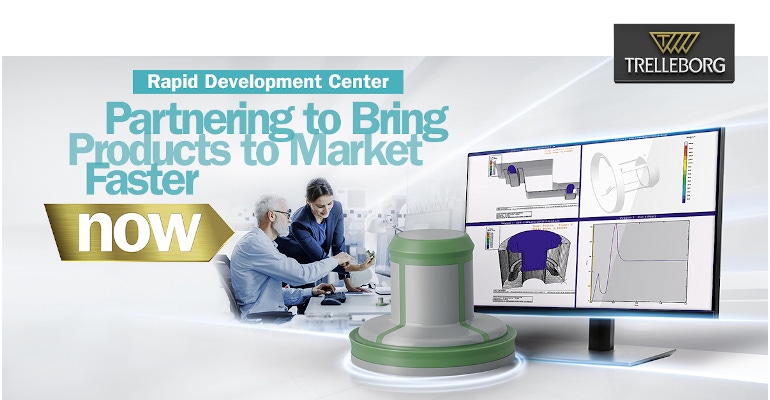
Product design can have a huge impact on manufacturing cost. “Somewhere between 80% and 90% of the manufacturing cost is typically designed into a product,” Andrew Gaillard, global director, Trelleborg Healthcare & Medical, told MD+DI during an interview at MD&M West 2021.
Gaillard said that he and his team have been asked by customers to identify ways to take cost out of medtech products. Trelleborg supplies high-performance silicone materials and molds, and extrudes silicones and some thermoplastics. The company also provides silicone that can be impregnated with active pharmaceutical ingredients. Trelleborg has been expanding its services by offering sourcing and assembly. And to help support cost efficiency, the company is now launching its Rapid Development Center.
Chris Tellers serves as director of the Rapid Development Center. “Working with our customers earlier in the product development cycle enables us to help them save time, reduce costs, and produce higher-quality parts; all while keeping in mind the long-term goal of serial production,” he said in a statement. “Employing Design for Manufacturing (DfM) principles ensures processes are efficient and cost-effective in high volumes, helping to alleviate the manufacturing costs that are often designed into a product.”
The new center enables Trelleborg to take a medtech project from design to production, globally. It also facilitates customer access to experts in DfM, materials, injection molding and assembly processes, and quality, said Gaillard. “Our team of experts can provide customers a huge advantage,” he said. “They know what works in a manufacturing environment because they spent years on the floor experiencing it. Having that kind of qualified support provides is invaluable to our customers.”
An extensive tool shop enables Trelleborg to quicky produce tooling. Tellers and his team can produce a sample prototype in as fast as 24 hours, while some can take 3 to 6 days, depending on the complexity of the part, Gaillard said. The company has opted for steel tooling inserts that can be produced quickly, rather than the more common approach to quick-turnaround tooling, aluminum. “Sometimes aluminum tools only last for a few prototypes,” said Gaillard, which could limit the number of samples for testing and evaluation.
Trelleborg’s expanding service support may also help medical device companies with another request—supplier consolidation. “Customers are saying they want to consolidate suppliers and have strategic suppliers provide more support than they do today,” Gaillard said. In addition to increasing its services offering, Trelleborg is in the process of standardizing its quality systems and automation across its facilities. “The goal would be for customers to qualify one location and then our standardization would allow them to use our other locations,” he said.
The Rapid Development Center had its soft launch with a few customers in late July and is now ready for operations. Tellers said in the statement that the center will enable Trelleborg to “take a consultative approach to help customers discover what they need and how it can be realized. Trelleborg has multiple decades of experience manufacturing silicones, thermoplastics, and metals. Our experts leverage their expertise, look at complex designs, and quickly create prototypes and tooling that help customers achieve their goals.”
The Trelleborg Healthcare & Medical Rapid Development Center offers design consultation, toolmaking, prototyping, high-precision machining, silicone molding, thermoplastic molding, automation, Class 7 cleanrooms, assembly, and secondary operations. Customers are also supported with raw material traceability and established validation processes. Trelleborg’s Healthcare & Medical facilities are ISO 13485:2016 and ISO 9001 certified and meet requirements from the FDA and the European Medical Device Regulation.
To learn more about the Rapid Development Center, visit here.
About the Author(s)
You May Also Like