Packaging
Packaging Visionary in Pharma Medtech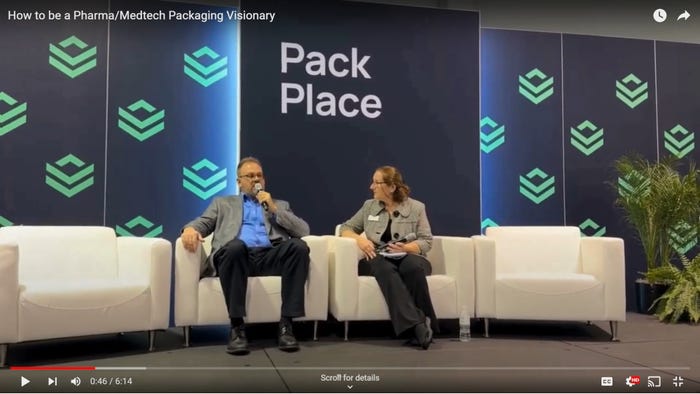
Packaging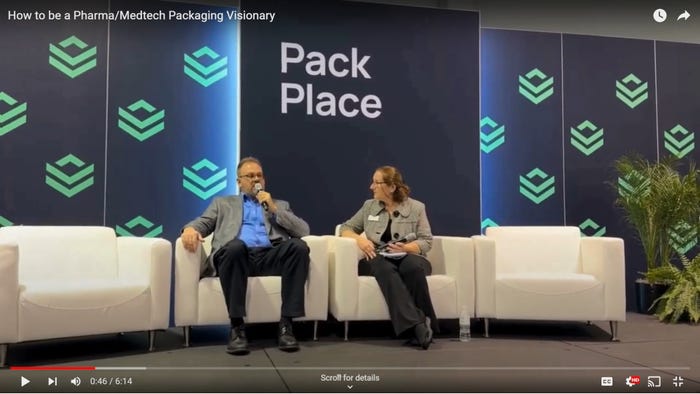
How to be a Packaging Visionary in Pharma and MedtechHow to be a Packaging Visionary in Pharma and Medtech
Here’s how you can be the leader you’ve always wanted to be, even within the prescribed limits of industry regulations.
Sign up for the QMED & MD+DI Daily newsletter.