Behind the Design of the Orchid Safety Release Valve
A behind-the-scenes look at the design inputs, challenges, and breakthrough moments in a quest to create a tension-activated safety release valve for medical tubing applications.
February 27, 2024
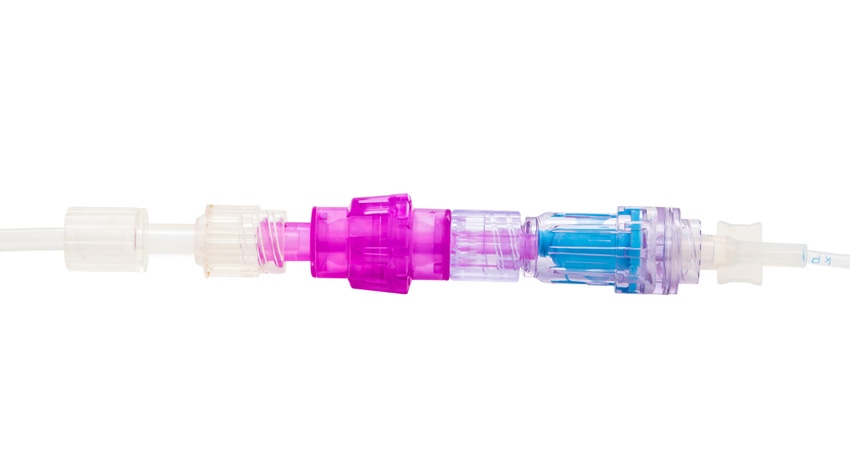
At a Glance
- Linear was recently awarded a contract with the U.S. Department of Veteran's Affairs for the Orchid SRV.
- The Orchid SRV was designed to prevent accidental dislodgement of IV catheters.
- The company is also working on a similar device for use in surgical/wound, nephrostomy, and abscess drainage tubing.
Every medical device engineer likely has that one project that's both challenging and interesting enough to stick with them long after it's completed.
For John Hayes, director of integrated systems at Gilero, that project is a tension-activated breakaway safety release valve (SRV) marketed as the Orchid SRV and sold by Linear Health Sciences.
"This was the best puzzle I've ever had in my career," Hayes told MD+DI.
The Orchid SRV was designed to tackle the all-too-common problem of accidental medical tubing dislodgement, beginning with IV catheters.
Before partnering with Gilero, Linear Health Sciences had an early prototype device, but design flaws and technical challenges led the company to seek outside help. A mutual friend in the industry introduced Linear's team to Gilero, a contract manufacturing and design firm specializing in medical device and drug delivery systems.
"We quickly realized they were the right partner to understand the intricacies of these types of products," Dan Clark, co-founder and CEO at Linear, told MD+DI.
Simple but elegant
The beauty of the Orchid SRV is in how simple it is to use without imposing any new educational requirements on the nursing staff. And yet, the inner workings of the device are far more complex.
"There are a lot of mechanical interactions that are occurring within that split second of disconnection, and they all need to be working together," Hayes said. "You have 1-degree of freedom, which is that pure tension, and so you need to find a mechanical balance that permits you to have the rigidity, yet flexibility in the design to disconnect at a predetermined threshold. And so, it’s a simple design, but it’s elegant in that you have all these interactions that are preventing it from moving in degrees of freedom that you want to constrain. ... You only want to act in that axial direction along the patient line."
A shared passion for the project
Clark shared one of his favorite stories from working with Gilero, and Hayes in particular.
"There was one night that this project kept John up late at night," Clark said. "... I got a phone call, and I was in California at the time, John was on the East Coast."
Hayes called Clark at 3 am Pacific Time, which was 6 a.m. Eastern Time. Hayes had been up all night trying to solve a technical conundrum and had finally had a breakthrough moment in which he figured out how to make the valve work within the specified constraints by incorporating a petal-like mechanism.
"The reason they're the perfect partner, and specifically John, is because he shared that passion; he shared the vision," Clark said. "He called me and said, 'I don't care what time it is, we have to talk about this.'"
For a small company like Linear Health Sciences, knowing that your design partner shares that passion for reaching a specified goal is priceless.
Design and engineering takeaways
Speaking with MD+DI’s engineering audience in mind, Hayes emphasized the importance of understanding the manufacturing process and injection molding. “When you’re trying to solve a problem like this, you can’t just think about it in terms of limitations on your CAD modeling experience or even just your mechanical design experience,” he said. “You have to have an understanding of the molding process because we had to work within some constraints, but we also pushed a few boundaries, and it enabled us to produce a design that was free of imperfections in areas that were going to be important to interact with each other to produce the desired outcome.”
And of course, human factors are another important consideration. For example, it was important for patient safety that the Orchid SRV be designed in a way that prevented reuse once the valve is disconnected.
“I was inspired a bit by some experience working on needle safety devices where you have two energy states and you’re going from one energy state to the next energy state, and, trying to get back to that first energy state there’s no features that the human hand is capable of manipulating without some sort of tool to reset the device,” Hayes said.
Linear recently scored a contract with the U.S. Department of Veteran's Affairs (VA) and GS2 (Government Solutions and Services) allowing the VA system to evaluate and adopt the Orchid SRV.
The company has also received an Innovative Technology contract from Vizient for the Orchid SRV and a national group purchasing agreement with Premiere.
About the Author(s)
You May Also Like